About Us
At HydroForce™ Pumps Ltd we are a family owned pump development and manufacturing company
in the heart of the UK. HydroForce™ Pumps Ltd is part of the same family as Rainwater Harvesting Limited
- one of the UK's leading rainwater harvesting specialists.
See below for an overview on the HydroForce™ Series 3's development and high quality manufacturing.
Early in 2009 the research and development team at HydroForce™ Pumps Ltd focused their efforts to produce a highest quality pump with unsurpassed levels of reliability.
Starting with sketches, the pump went through a great scrutiny to ensure a design that would give years of trouble free running. Components were tested to extremes, and prototypes were meticulously assessed and logged.
Down to the smallest of components, development continued until the team were assured outstanding
levels of performance and reliability could be categorically guaranteed.
In all, over 100 pumps were made for testing and development processes.
The picture shows the evolution of the patented alloy bulkhead (creating a twin chamber design prevents ingress of water to motor, electrical components and to bearing oil.) This componant alone went through around 10 prototypes before a go-ahead was given to the toolmakers to produce tooling.
The LTB (longterm test bed) has tested a single pump through over 18,000 cycles- pumping 70L twice an hour for nearly two years. This replicates around 25 years usage for a gravity feed rainwater harvesting system it is designed to service.
Production
The HydroForce™ Series 3 enjoys its own production line at its UK based factory.
All components used within the pump have been sourced with the ground rules that quality is the important factor. Most components are sourced from a 100 mile radius of the factory.
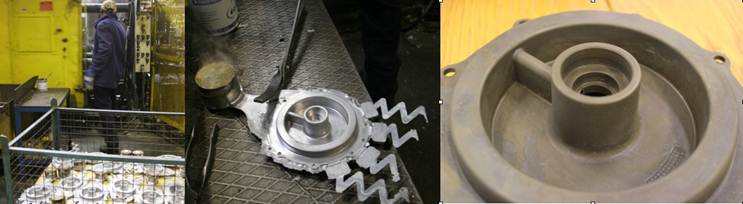
For example the patented plate is manufactured by a process of high pressure aluminium die casting. This
guarantees the plates are within tolerances of 0.001 mm and the size critical parts need no machining.
The material itself is the highly corrosion resistant 70L aluminium- then anodised to further guarantee
any possibility of corrosion.
The above picture shows the pump being casted, and on the far right the finished, anodised plate.
A clean, clear and technologically advanced production like make the manufacturing process fast, efficient
and reduces the likelihood of errors. Where possible, processes are automated- below shows the crucial screws
being inserted to hold the pressurised zones together. A system has been put into place to automatically
tighten the screws to the correct torque- preventing splitting the casing if too tight or ingress of water
if too loose.
All pumps go through a rigorous testing programme. First the pumps are subjected to a 4 stage electrical test using the latest in electrical testing equipment.
The pumps have their pressure and flow rate tested twice at different stages of assembly. the performance of each pump is automatically logged against its bar code number to assure the client of its quality.
The HydroForce™ Series 3 is now enjoying unsurpassed reliability rates and is being exported worldwide.